Basic Testing
The purpose of testing was to compare the project with original design.
​
Dimensional testing: before installed solar-tracker, checked and ensured the size and weight of parts were met the design requirements.
Install testing: at the beginning of the testing part, the solar-tracker should be built completely. The solar panel can be installed to the frame, and motors can driver the solar panel in both horizontal and vertical direction. After finished the build of solar tracker, the two methods will be used for testing it in two different places.
Angle and tolerance testing: the first place is inside the room, and the first method is Visual Observation method, which observe if the solar panel changes the position by eyes when use an electric torch to shoot the sensor panel from different angle. The second method is Math Calculate method, determine the length of shadow in the sensor panel and the size of shaft to calculate the tolerance angle that the solar tracker created, and the calculate way is the same as the analysis shown in analysis section.
Function testing: After those testing, the function testing will be taken in an open area in sunny day to test the same experiment again to make sure it works in real environment. And testing time will be 6 in the morning, 12 at noon, and 5 in the afternoon.
​
There were few basic testing above, dimensional testing and install testing that used to check the construction, and the angle and function testing that used to check if the program and motor work.
Main Testing
Introduction
Introduction:
The testing was focusing on three statements, panels needs to perpendicular to incoming sunlight 90 degrees, with 2 degrees deviation, increased around 20% energy flue in the surface from incoming sunlight by change position of solar panel, and the panel is able to rotate in both vertical and horizontal directions.
The testing was focusing on three statements, panels needs to perpendicular to incoming sunlight 90 degrees, with 2 degrees deviation, increased around 20% energy flue in the surface from incoming sunlight by change position of solar panel, and the panel is able to rotate in both vertical and horizontal directions.
Predicated performance:
Predicated performance:
The device will rotate both vertical and horizontal directions automatically and faces to incoming sunlight directly.
The device will rotate both vertical and horizontal directions automatically and faces to incoming sunlight directly.
All of angles during the testing had 50 tolerances, and 0.5 V tolerance for all data. The testing was repeat three times to take average to increase accuracy.
Step:
The purpose of the main testing was to figure out if the device was able to rotate both vertical and horizontal directions automatically and faces to incoming sunlight. There were four steps for testing​
-
Step 1: Connect Mini-Kit with motor and Arduino control chip
-
Step 2: Post the program to Arduino control chip
-
Step 3: Connect with power supplier and record the voltage values.
-
Step 4: Testing outside the building and record voltage value each hour
Parameter values:
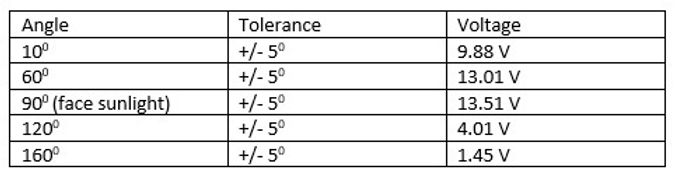
traditional solar panel:the power received increased until highest point and then decrease until minimum value in a day.

solar tracker that used time function to program, it increased the power received, but it had a large amount of angle tolerance. Therefore, the value in each hour was not close at all.
Issue and solve:
During the testing, there was a issue that the motor could move over based if used time function to program and control the motor. And some small sensors were added to check the voltage difference, so the motor can move based on the voltage difference on the side instead of time.